Have you ever wondered why rockets have nozzles?
Well, the answer lies in the basics of rocket propulsion. Rockets generate thrust by expelling high-speed gases out of their engines. And it is the nozzle that plays a crucial role in this process.
The nozzle design and shape are carefully engineered to maximize the efficiency and performance of rockets. By accelerating and expanding the exhaust gases, the nozzle helps convert the energy released from burning propellants into forward motion.
Additionally, nozzles can be designed to provide thrust vectoring, allowing rockets to change direction during flight.
However, designing effective rocket nozzles is not without its challenges and limitations. Future developments in rocket nozzle technology aim to overcome these obstacles and further improve space exploration capabilities.
So, join us as we delve deeper into the fascinating world of rocket nozzles and uncover their significance in powering our journey beyond Earth’s atmosphere.
The Basics of Rocket Propulsion
You might be wondering why rockets have nozzles, but they are actually essential for rocket propulsion. The nozzle plays a crucial role in the functioning of a rocket engine.
Rocket propulsion relies on the principle of Newton’s third law of motion, where for every action there is an equal and opposite reaction. The nozzle helps to accelerate and expel the high-speed exhaust gases produced by the combustion process, generating the necessary thrust for the rocket to overcome gravity and travel through space.
How Rockets Generate Thrust
When it comes to generating thrust, combustion plays a crucial role in rocket propulsion. By burning fuel and oxidizer together, rockets release large amounts of energy in the form of expanding gases.
These expanding gases are essential for creating the force necessary to propel the rocket forward.
Nozzles also play a vital function as they help accelerate and direct the flow of these gases, increasing their velocity and maximizing thrust.
The Role of Combustion
The crucial role of combustion in rockets necessitates the presence of nozzles. Combustion occurs within the rocket engine, where fuel and oxidizer are mixed and ignited to produce high-pressure gases. These gases expand rapidly, generating thrust through Newton’s third law of motion.
The rocket nozzle plays a vital role in this process. It efficiently converts the high-pressure gas into high-velocity exhaust flow, maximizing thrust and improving overall rocket performance.
Some benefits of having a well-designed nozzle include increased efficiency, optimal thrust-to-weight ratio, enhanced propulsion system, improved payload capacity, and higher altitude attainability.
The Importance of Expanding Gases
Expanding gases play a crucial role in rocket propulsion by driving high-velocity exhaust flow, maximizing thrust and improving performance. The importance of expansion lies in the fact that it converts the energy released during combustion into kinetic energy. This acceleration is achieved through a nozzle, which efficiently expands the gases and increases their velocity. The table below illustrates the relationship between gas expansion ratio and its effect on thrust and specific impulse.
Expansion Ratio | Thrust (increase/decrease) | Specific Impulse (increase/decrease) |
---|---|---|
High | Increase | Increase |
Low | Decrease | Decrease |
By optimizing the expansion ratio, rocket designers can enhance overall efficiency and achieve greater mission success.
The Function of Nozzles
Get ready to learn how nozzles work and why they’re essential for maximizing rocket performance!
Nozzles play a crucial role in directing the flow of expanding gases released by the rocket’s engine.
The shape of the nozzle greatly impacts thrust efficiency, as different shapes can either increase or decrease exhaust velocity.
Additionally, nozzle materials are carefully selected to withstand high temperatures and pressures, ensuring optimal performance during the intense conditions of rocket propulsion.
Nozzle Design and Shape
When discussing nozzle design and shape, there are three key points to consider: convergent-divergent nozzles, bell nozzles, and plug nozzles.
Convergent-divergent nozzles are designed to accelerate the exhaust gases. They achieve this by gradually increasing the area of the nozzle as the gases expand.
Bell nozzles, on the other hand, have a curved shape. This shape allows for better expansion of exhaust gases at high altitudes.
Finally, plug nozzles feature a cylindrical section followed by a conical section. This design helps in achieving higher efficiency at different altitudes and pressures.
These different nozzle designs and shapes play a crucial role in optimizing the performance of various systems and applications.
Convergent-Divergent Nozzles
The convergent-divergent nozzle design propels rockets with incredible power. Its efficiency is crucial for achieving high rocket performance. It allows for the expansion and acceleration of exhaust gases, increasing thrust. This design is especially effective in supersonic flow conditions, optimizing supersonic nozzle performance.
The divergent section of the nozzle expands the flow, converting thermal energy into kinetic energy and maximizing propulsion efficiency.
Bell Nozzles
Bell nozzles enhance rocket engine performance by efficiently expanding exhaust gases to maximize thrust. Their unique shape and design allow for a gradual increase in area along the length of the nozzle, optimizing the expansion process. This results in higher nozzle efficiency and improved overall engine performance.
The bell shape of these nozzles also helps mitigate some of the loss in thrust caused by atmospheric pressure variations during ascent and descent phases.
Plug Nozzles
Plug nozzles offer an incredible efficiency and performance boost. Their unique design optimizes exhaust gas expansion and mitigates the impact of atmospheric pressure variations during ascent and descent phases.
Typically made from high-strength materials like carbon composites or refractory metals, plug nozzles can withstand extreme temperatures. These materials also provide thermal protection by preventing heat transfer to other parts of the rocket engine, ensuring its structural integrity.
Thrust Vectoring
Rocket nozzles are designed to allow for thrust vectoring, which means they can be adjusted to change the direction of the rocket’s propulsion. This capability is crucial for precise control and maneuverability during flight. By altering the angle of the nozzle, the thrust can be redirected, enabling the rocket to change its course or maintain stability. Thrust vectoring enhances maneuverability and improves nozzle efficiency by optimizing propulsion direction.
The incorporation of thrust vectoring technology allows rockets to navigate through various flight conditions with greater accuracy and responsiveness. It enables them to overcome challenges such as wind gusts or unexpected obstacles encountered during launch or in space. Additionally, this capability ensures that rockets can efficiently utilize their propellant by directing thrust precisely where it is needed most.
Efficiency and Performance of Nozzles
By optimizing the design of their nozzles, engineers can significantly enhance the efficiency and performance of propulsion systems. This is achieved through various techniques, such as expanding the nozzle to increase exhaust velocity and improve thrust efficiency.
Additionally, by carefully shaping the nozzle contours, engineers can reduce losses caused by shockwaves and increase overall engine performance. These efficiency improvements and performance optimizations are crucial in maximizing rocket capabilities.
Challenges and Limitations of Nozzle Design
Now let’s delve into the challenges and limitations faced in designing rocket nozzles.
Despite their crucial role in propulsion efficiency, nozzle design is not without its obstacles. Engineers must grapple with complex fluid dynamics, high temperatures, and extreme pressures.
The challenge lies in achieving optimal expansion ratios while balancing structural integrity and weight constraints.
These limitations necessitate careful consideration of materials, cooling mechanisms, and manufacturing processes to ensure safe and efficient operation of rocket engines.
Future Developments in Rocket Nozzle Technology
Imagine the exciting possibilities that lie ahead as advancements in rocket nozzle technology continue to push the boundaries of propulsion efficiency and performance.
With ongoing research, engineers are exploring new rocket nozzle materials and innovative cooling techniques to optimize rocket engine performance.
By developing materials that can withstand extreme temperatures and pressures, such as carbon composites or advanced ceramics, and implementing efficient cooling methods like regenerative cooling or film cooling, future rocket nozzles will be able to operate at higher thrust levels for longer durations.
These advancements in rocket nozzle technology will not only improve the overall efficiency of rocket engines but also enable the development of more powerful and capable launch vehicles.
Additionally, future developments may also include the use of additive manufacturing techniques to fabricate complex nozzle geometries, further enhancing performance and reducing manufacturing costs.
Overall, the future of rocket nozzle technology holds immense potential for revolutionizing space exploration and enabling humans to reach new frontiers in the cosmos.
The Role of Nozzles in Space Exploration
Rocket nozzles play a vital role in space exploration, propelling spacecraft with incredible force and precision. The efficiency of rocket nozzles is crucial for achieving optimal performance and reducing fuel consumption.
Advancements in nozzle technology have focused on improving the design and materials used, resulting in increased thrust and higher exhaust velocities. These advancements have allowed for more efficient propulsion systems, enabling longer missions and the exploration of distant celestial bodies.
Frequently Asked Questions
How do rockets generate thrust in the absence of an atmosphere?
In the absence of an atmosphere, rockets generate thrust through rocket propulsion. Rocket engines work by expelling high-speed exhaust gases in one direction, which creates a reaction force in the opposite direction. This is known as Newton’s third law of motion.
By burning fuel and oxidizer together in a combustion chamber, the resulting hot gases are accelerated and forced out of the rocket nozzle at high velocities. This propels the rocket forward and allows it to overcome Earth’s gravity.
What is the purpose of thrust vectoring in rocket propulsion?
Thrust vectoring is a crucial aspect of rocket propulsion. It allows for precise control and maneuverability. By altering the direction of thrust, rockets can adjust their trajectory, counteract external forces, and maintain stability.
This technology finds applications in various fields, including aerospace and defense. The benefits of thrust vectoring are numerous. It improves efficiency, increases payload capacity, enhances safety during launch and reentry, and enables the performance of complex maneuvers in space.
Overall, thrust vectoring plays a vital role in rocket propulsion, enabling rockets to achieve their intended objectives with precision and reliability.
How do nozzle design and shape affect the performance of a rocket?
Nozzle design and shape have a significant impact on the performance of a rocket. The expansion ratio, throat area, and contour of the nozzle all influence the flow velocity, pressure distribution, and exit velocity of the exhaust gases.
A well-designed nozzle allows for the optimal expansion of high-pressure gases, effectively converting their thermal energy into kinetic energy. This efficient conversion results in increased thrust output and improved overall rocket performance.
Engineers carefully consider these factors to maximize thrust while minimizing propellant consumption. By doing so, they can enhance the efficiency and effectiveness of the rocket, ultimately achieving better performance.
What are the challenges and limitations faced in designing rocket nozzles?
When designing rocket nozzles, there are several challenges and limitations to consider.
One of the main challenges is achieving efficient propulsion while maintaining structural integrity. The nozzle must withstand the extreme temperatures and pressures generated during launch.
Optimizing the shape can be complex as it involves balancing factors such as thrust, exhaust velocity, and weight constraints.
Furthermore, manufacturing techniques must be precise to ensure accurate dimensions and smooth interior surfaces for optimal performance.
Are there any upcoming advancements or future developments expected in rocket nozzle technology?
Upcoming advancements and future developments in rocket nozzle technology are expected to focus on enhancing efficiency and performance.
Researchers are exploring innovative materials, such as carbon nanotubes, for their ability to withstand extreme temperatures and pressures.
Additionally, novel designs like aerospike nozzles are being investigated to optimize thrust at various altitudes.
Advanced manufacturing techniques like 3D printing may also play a pivotal role in producing intricate nozzle geometries for improved propulsion systems.
These advancements aim to revolutionize space exploration by maximizing thrust while minimizing fuel consumption.
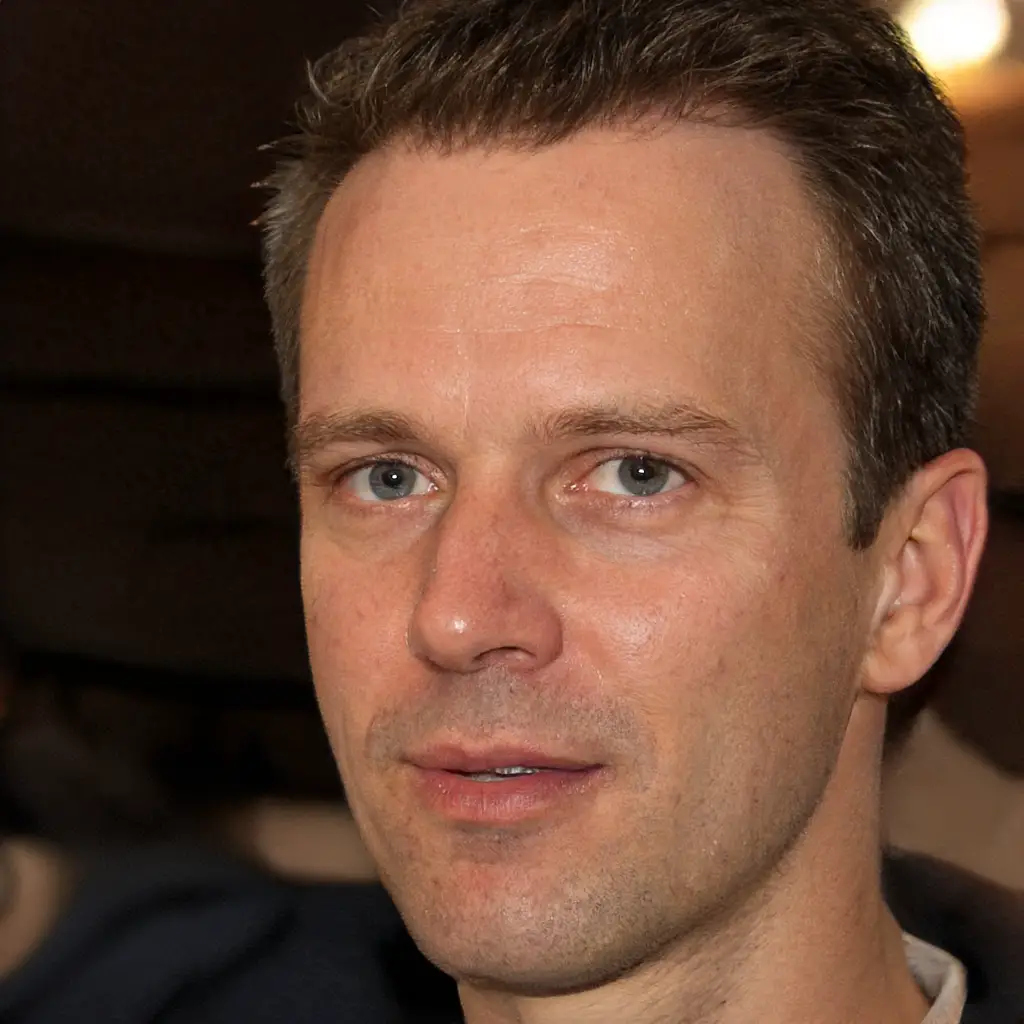
I’m Carlos Robert, a passionate gardener, and blogger. With years of experience and knowledge in the field of garden watering, I have created a blog to share my insights and tips on the topic. I strive to provide readers with detailed information about all aspects of sprinkler systems, from garden sprinklers to fire sprinklers, along with nozzles, hoses, and other related products. I love helping my readers create the perfect garden with their ideal setup!