Water hammer in sprinkler systems is a hydraulic shock caused by rapid valve closure, high water pressure, or trapped air in pipes. This can lead to pipe damage, valve failures, and safety risks. Water hammer arrestors mitigate these effects by absorbing shock waves and pressure spikes, hence protecting the system and reducing noise. They employ mechanisms such as pistons or diaphragms and should be correctly installed near quick-closing valves.
Proper installation, maintenance, and compliance with safety standards are crucial for peak system performance. For in-depth knowledge, a detailed understanding of underlying technologies and best practices is essential.
Understanding Water Hammer in Sprinkler Systems
Water hammer in sprinkler systems occurs when rapid valve closures cause sudden stops in water flow, generating pressure waves that reverberate through the pipes.
This phenomenon can be attributed to high water pressure, undersized pipes, and trapped air within the system.
The resulting effects include loud banging noises and potential damage to plumbing infrastructure, necessitating effective mitigation strategies.
What Is Water Hammer?
In sprinkler systems, the phenomenon of water hammer occurs when the rapid closure of valves causes a sudden halt in water flow, generating a pressure wave that travels through the pipes. This water hammer effect results in a pressure surge that can exert significant stress on the irrigation valves and PVC piping.
Particularly in an automatic irrigation system, where fast-acting solenoid valves are prevalent, the abrupt changes in water flow can lead to substantial vibrations and loud banging noises.
The pressure surge travels at high speed, often near the speed of sound in water, and can cause repeated shock waves through sprinkler zones. This can compromise the integrity of the system, necessitating robust water pressure regulation and pipe damage prevention measures.
A backflow preventer may also be impacted by these pressure waves, further complicating the system’s stability.
To mitigate these risks, shock absorber devices, such as water hammer arrestors, are used. These devices are strategically placed near problem valves to absorb the energy of the pressure waves, minimizing the potential for pipe damage and prolonging the lifespan of the irrigation system.
Proper installation and maintenance of these devices are important for effective water hammer management.
Causes of Water Hammer in Sprinkler Systems
Rapid valve closure, particularly in automatic irrigation systems with fast-acting solenoid valves, stands as one of the primary causes of water hammer in sprinkler systems. This sudden cessation of water flow creates a pressure wave that reverberates through the piping network, leading to potentially damaging surges.
High water pressure exacerbates these issues, magnifying the intensity of the pressure waves. Similarly, undersized pipes force water to travel at higher velocities, increasing susceptibility to water hammer. Air trapped in pipes introduces another variable; air pockets can accelerate flow changes, further destabilizing the system.
Pump operation, especially abrupt starts and stops, can also induce water hammer by causing rapid changes in flow dynamics. Water column separation, where water columns split and recombine, can lead to significant pressure shocks. Poorly secured pipework adds to the problem, as vibrations from pressure waves can cause physical damage over time.
Multiple valve operation, where several valves close simultaneously, compounds these effects, creating more severe pressure fluctuations. Lastly, wear of valve components over time can degrade their performance, making them more prone to rapid closure and subsequent water hammer.
Understanding these water hammer causes is essential for effective system design and maintenance.
Effects of Water Hammer on Plumbing and Sprinklers
Understanding the causes of water hammer in sprinkler systems is essential, as the resulting pressure surges can inflict significant damage on plumbing and irrigation components. These sudden pressure spikes can lead to pipe damage, causing cracks, ruptures, or even bursts, particularly at joints and fittings. Such damage can result in leaks and substantial water damage. Additionally, the shock waves from water hammer often loosen pipe connections, leading to joint failures and leaks.
Valve damage is another critical issue; repeated water hammer events can cause valves to leak or fail prematurely, compromising the system’s integrity. Fixture damage, affecting faucets, shower heads, and sprinkler heads, is also common, reducing their lifespan or causing immediate failure. This, in turn, can lead to reduced water pressure, impacting the efficiency of the water distribution system.
Water hammer not only accelerates the wear on all system components but also introduces safety hazards by potentially causing pipe bursts and fixture failures.
Effective water hammer prevention strategies include using pipe vibration dampers, water pressure regulators, and pressure surge mitigation techniques to enhance water distribution system optimization and minimize maintenance costs. Regular inspections are essential to maintaining system integrity and preventing these detrimental effects.
The Science Behind Water Hammer Phenomenon
When a valve in a piping system is suddenly closed, the resulting hydraulic shock phenomenon, known as water hammer, is driven by the momentum and inertia of the moving water. This abrupt halt in water flow generates a pressure wave that propagates through the pipe at the speed of sound in water, approximately 1,370 m/s.
As the pressure wave travels, it encounters changes in pipe geometry and closed ends, leading to the reflection of pressure waves, which can amplify the water hammer phenomenon.
The importance of pipes plays a vital role by allowing the pipe material to expand slightly under pressure, temporarily storing energy which is released as the pressure wave passes. In severe cases, this can lead to cavitation, where pressure drops cause vapor bubbles to form and collapse, further damaging the piping system.
Resonance occurs when the frequency of pressure waves aligns with the natural frequency of the piping system, amplifying pressure spikes that can exceed the pipe’s pressure rating. The kinetic energy of the moving water is converted into pressure energy during sudden flow stoppage, emphasizing the significance of proper pipe sizing.
Accurate pipe sizing and system design can mitigate these effects, ensuring the longevity and reliability of the plumbing infrastructure.
Importance of Water Hammer Arrestors in Sprinkler Systems
The importance of water hammer arrestors in sprinkler systems is underscored by their ability to absorb shock waves and mitigate pressure spikes, thereby preventing damage to system components and reducing noise.
These devices function through a chamber with a piston or diaphragm that compresses air to dissipate energy, and they come in various types and sizes suited for different applications.
The benefits of installing water hammer arrestors include extended system longevity, improved performance, and compliance with plumbing codes.
How Water Hammer Arrestors Work
Water hammer arrestors operate by using a chamber with a piston or diaphragm to compress air and absorb the shock waves caused by sudden changes in water flow, thereby safeguarding sprinkler systems from pressure-induced damage. These devices function as hydraulic shock absorbers, providing pressure surge protection and water pressure surge control. The piston or diaphragm inside the arrestor moves in response to pressure spikes, acting as a pipe shock absorber that mitigates the effects of water hammer.
In technical terms, water hammer arrestors serve as water hammer preventers, pressure spike dampers, and hydraulic shock control devices. When a sudden stop in water flow occurs, the piston or diaphragm compresses the air in the chamber, dissipating the energy and reducing pressure fluctuations, thereby acting as a water hammer suppressor. This process minimizes pipe vibration and helps maintain system stability.
Component | Function |
---|---|
Piston/Diaphragm | Moves to compress air, absorbing shock waves |
Chamber | Contains air or gas, which acts as a cushion |
Air Cushion | Absorbs and dissipates energy from pressure surges |
Sealed Design | Guarantees longevity and effectiveness of the arrestor |
Benefits of Installing Water Hammer Arrestors
Installing water hammer arrestors in sprinkler systems offers significant benefits, including noise reduction, enhanced system longevity, and improved efficiency. These devices are essential for mitigating the adverse effects of water hammer, a phenomenon that generates pressure waves capable of damaging plumbing infrastructure.
The primary advantage of a water hammer arrestor is noise reduction. By absorbing pressure spikes, these devices eliminate the loud banging sounds often heard when valves close quickly. This leads to a quieter and more comfortable environment.
In terms of pipe protection, water hammer arrestors safeguard against damage to pipes, fittings, and joints. This preventive measure is important for extending the lifespan of the entire irrigation system. Additionally, arrestors contribute to leak prevention, reducing the likelihood of leaks that result from repetitive stress on plumbing connections.
Improved appliance performance is another significant benefit. Water hammer arrestors help maintain consistent pressure levels, thereby protecting sensitive components in appliances and enhancing their operational longevity.
System efficiency is also significantly increased, as pressure stabilization helps optimize water flow and reduces energy consumption, contributing to energy conservation. Additionally, these devices offer safety enhancement by minimizing the risks of pipe bursts or fixture failures.
Water hammer arrestors adhere to code compliance requirements, are easy to install, and offer a maintenance-free solution, making them an indispensable component in modern sprinkler systems.
Types of Water Hammer Arrestors
Various types of water hammer arrestors, each with unique mechanisms and characteristics, are essential for effectively mitigating pressure surges in sprinkler systems. Understanding these types is vital for selecting the appropriate solution to guarantee excellent hydraulic shock protection and system longevity.
The primary types of water hammer arrestors used in plumbing systems include piston-type, diaphragm-type, bellows-type, single chamber arrestors, mini end stop arrestors, and hose bib style arrestors. Each type employs different methods to absorb the pressure surges generated by quick-closing valves in sprinkler systems.
Type of Arrestor | Key Characteristics |
---|---|
Piston-type | Uses a piston to compress an air cushion |
Diaphragm-type | Employs a flexible diaphragm to separate water from the air chamber |
Bellows-type | Utilizes a bellows instead of a diaphragm |
Single chamber arrestors | Features a sealed air chamber for absorption |
Piston-type arrestors are ideal for long-term use due to their sealed units that maintain the air cushion indefinitely. Diaphragm-type arrestors offer a flexible solution by separating the water and air chambers with a diaphragm. Bellows-type arrestors provide similar functionality using a bellows mechanism. Single chamber arrestors are typically used for smaller pipe sizes and provide efficient shock absorption. Mini end stop arrestors and hose bib style arrestors cater to specific installation needs, such as appliance connections and high water volume scenarios, respectively.
Selecting the appropriate type of water hammer arrestor depends on pipe size, system pressure, and specific application requirements, ensuring effective hydraulic shock protection.
Designing Sprinkler Systems to Minimize Water Hammer
In designing sprinkler systems to minimize water hammer, ensuring proper pipe sizing is paramount to maintaining ideal water velocity and preventing pressure surges. Effective pipe sizing aids in plumbing noise reduction and enhances the performance of the water hammer arrestor sprinkler system. Maintaining water velocities below 5 feet per second is essential for hydraulic shock suppression and pipe surge protection.
Here are four critical considerations:
- Valve Selection and Placement: Utilize slow-closing valves and install them close to sprinkler heads to control water flow and pressure surges, thereby improving the efficiency of sprinkler system components.
- Pressure Control: Integrate water pressure stabilizers and pressure-regulating valves to ensure consistent pressure throughout the system, thereby enhancing pressure surge control and reducing the risk of hydraulic shock.
- Air Management: Implement air relief valves at high points and air vents on mainlines to prevent air entrapment, which can disrupt water flow control and exacerbate hydraulic shocks.
- Pipe Support and Anchoring: Secure pipes with proper supports and use thrust blocks at direction changes to absorb forces, promoting effective hydraulic shock arrestors and pipe shock arrester functionality.
These design strategies collectively enhance the longevity and reliability of the sprinkler system while minimizing the adverse effects of water hammer.
Water Hammer Arrestor Sprinkler System: Components and Installation
A water hammer arrestor system comprises essential components including the arrestor device, fittings, and optional valve boxes for underground installations. Proper installation techniques involve selecting the correct size and ensuring secure connections, while placement considerations focus on positioning the arrestor within 6 feet upstream of quick-closing valves to maximize effectiveness.
Key Components of a Water Hammer Arrestor System
The key components of a water hammer arrestor system encompass the water hammer arrestor device itself, various fittings, valves, pipes, pressure gauges, and additional accessories such as valve boxes and pressure regulators. These components collaborate to mitigate the destructive pressure waves that cause water hammer.
Water Hammer Arrestor Device:
• Main component that absorbs shock waves.
• Contains a chamber with compressed air or gas.
• Equipped with a piston or diaphragm to separate air from water.
• Includes sealing O-rings in piston-type models.
Fittings:
• Threaded or flanged connections for attaching the arrestor to pipes. • Tee or elbow fittings for branching off the main pipe.
Valves:
• Shut-off valves to isolate sections during installation.
• Quick-closing valves like solenoid valves that trigger water hammer.
Pipes and Accessories:
• Main supply lines and branch lines to fixtures.
• Pressure gauge to monitor system pressure.
• Schrader valve for pressure adjustment on some models.
• Valve box for accessible underground installations.
• Pipe cutter for precise cuts in existing systems.
• Pressure regulator to control overall system pressure.
• Air relief valves to expel trapped air.
Proper sizing and strategic placement of these components guarantee the system’s effectiveness in dampening pressure surges and protecting the irrigation infrastructure.
Proper Installation Techniques
When properly installed, water hammer arrestors can greatly mitigate the disruptive pressure surges caused by rapid valve closures in sprinkler systems. Key installation techniques are vital for ensuring effective performance and longevity of these anti-water hammer devices in landscape irrigation applications.
The installation should position the water hammer arrestor within 6 feet upstream of the quick-closing valves, aligning closely with sprinkler valves, which are primary culprits of water hammer. Selecting the correct size based on the system’s flow rate and pressure is essential, as is following the manufacturer’s orientation guidelines—whether vertical, horizontal, or angled. For secure connections, use thread sealant or Teflon tape, and in the case of PVC pipes, apply appropriate cement and primer.
Accessibility is an important consideration for sprinkler system maintenance. If the installation is underground, a valve box can facilitate future inspections and replacements. Larger irrigation systems may benefit from multiple arrestors, strategically placed at key points such as near valves and directional changes in piping.
Adjusting the internal pressure of the arrestor to 30-50% of the system’s normal working pressure can optimize performance. Finally, ensure compatibility with local plumbing codes and the system’s pressure and flow characteristics to safeguard building safety and promote water conservation.
Placement Considerations for Optimal Performance
Proper placement of water hammer arrestors is essential for maximizing their effectiveness in mitigating pressure surges in sprinkler systems. To achieve peak performance, several critical placement considerations must be adhered to.
Firstly, the water hammer arrestor should be installed as close to the source of the water hammer as possible, typically within 6 feet upstream of quick-closing valves in residential irrigation systems. This proximity ensures the arrestor can effectively absorb pressure waves generated by sudden valve closures.
Secondly, sizing the arrestor correctly is crucial. The appropriate size depends on the system’s flow rate and pressure. For instance, for 3/4′ service lines, a B size arrester is suitable, while a C size arrester is recommended for 1′ service lines. If the system pressure exceeds 55 psi, the arrester size should be increased by one.
Thirdly, consider the following placement considerations:
- Orientation: Install the arrestor vertically, horizontally, or at an angle, as specified by the manufacturer.
- Access: Use valve boxes for underground installations to facilitate maintenance.
- Multiple Points: In larger systems, place arrestors near valves and pipe direction changes.
- Local Plumbing Codes: Always comply with local requirements for installation.
Lastly, make sure the pressure setting is calibrated to 30-50% of the system’s normal working pressure, and account for potential system modifications during retrofitting.
Maintenance and Troubleshooting of Water Hammer Arrestors
Regular inspection and maintenance of water hammer arrestors are essential to ensuring the longevity and peak performance of your sprinkler system. Effective maintenance practices include periodic inspection, pressure testing, flushing, and addressing air pockets. Regularly check for visible signs of damage or leaks, and ensure connections remain tight. Use a pressure gauge to monitor system pressure, which should stay within 30-50% of the normal working range. Adjust system pressure as necessary using pressure-reducing valves.
Flushing the system helps remove debris that could clog arrestors. This involves running water through the system at high velocity to dislodge any buildup. If water hammer persists, it may indicate a failed arrestor that requires replacing. Consider upgrading to larger capacity units if problems continue.
Air pockets can compromise arrestor effectiveness. Bleed air from the system by opening the highest and lowest faucets, or install air release valves at high points. Adjusting valve closure speeds can also mitigate sudden pressure changes.
For peak performance, continually evaluate your system design, especially in cold climates, where winter maintenance is crucial to prevent freezing. Regular documentation of maintenance activities will assist in future troubleshooting.
Maintenance Task | Frequency | Key Considerations |
---|---|---|
Inspection | Periodically | Check for damage, leaks, secure connections |
Pressure Testing | Regularly | Maintain 30-50% of normal working pressure |
Flushing | Occasionally | Remove debris to prevent clogging |
Compliance and Safety Standards for Water Hammer Prevention in Sprinklers
While regular maintenance and troubleshooting are essential for the effectiveness of water hammer arrestors, adherence to compliance and safety standards is equally vital to guarantee the reliability and safety of sprinkler systems. Key compliance standards and safety guidelines for water hammer prevention include requirements from NFPA 13, UL standards, ANSI/ASABE S376.3, and general safety practices.
NFPA 13 Requirements:
• Minimum closure time of 5 seconds for control valves to mitigate pressure surges.
• Proper pipe sizing to maintain safe water velocities.
• Installation of pressure gauges for system monitoring.
UL Standards:
• UL 199 mandates water hammer tests to verify durability against pressure surges.
• UL 1821 sets requirements for thermoplastic sprinkler pipes and fittings.
ANSI/ASABE S376.3:
• Guidelines for safe design of underground thermoplastic irrigation pipelines.
• Recommendations on pipe sizing and material selection to control water velocity.
General Safety Guidelines:
• Install water hammer arrestors near quick-closing valves.
• Employ pressure regulators to control system pressure.
• Ensure proper pipe support and anchoring.
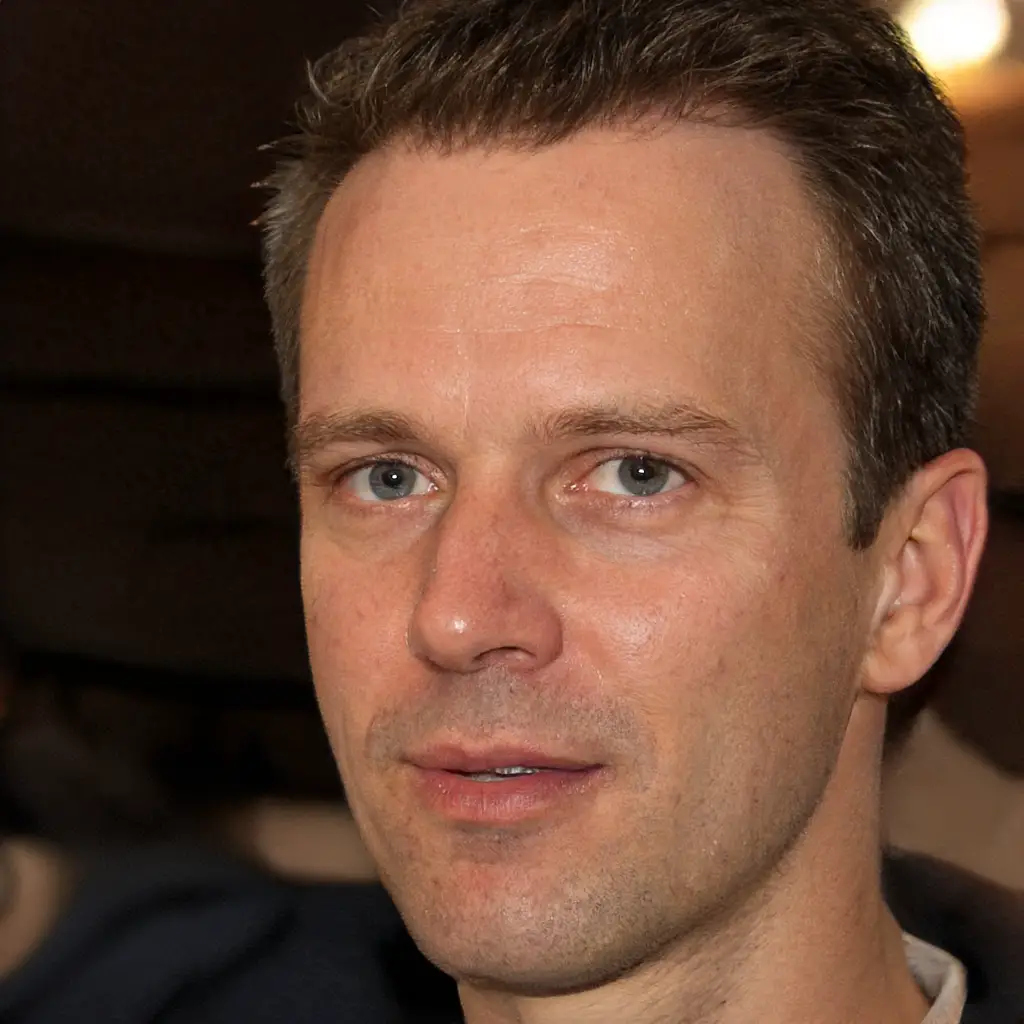
I’m Carlos Robert, a passionate gardener, and blogger. With years of experience and knowledge in the field of garden watering, I have created a blog to share my insights and tips on the topic. I strive to provide readers with detailed information about all aspects of sprinkler systems, from garden sprinklers to fire sprinklers, along with nozzles, hoses, and other related products. I love helping my readers create the perfect garden with their ideal setup!